Safety Approval
Tracer Gas Testing
Using the Conformity Discovery Process©
- Your Product Is Designed To Pass
- Quicker To Market
- More Cost Effective
We walk you through every step to get your safety approval: no need to be a Tracer Gas Expert with Tracer Gas Testing Equipment. We got it covered!
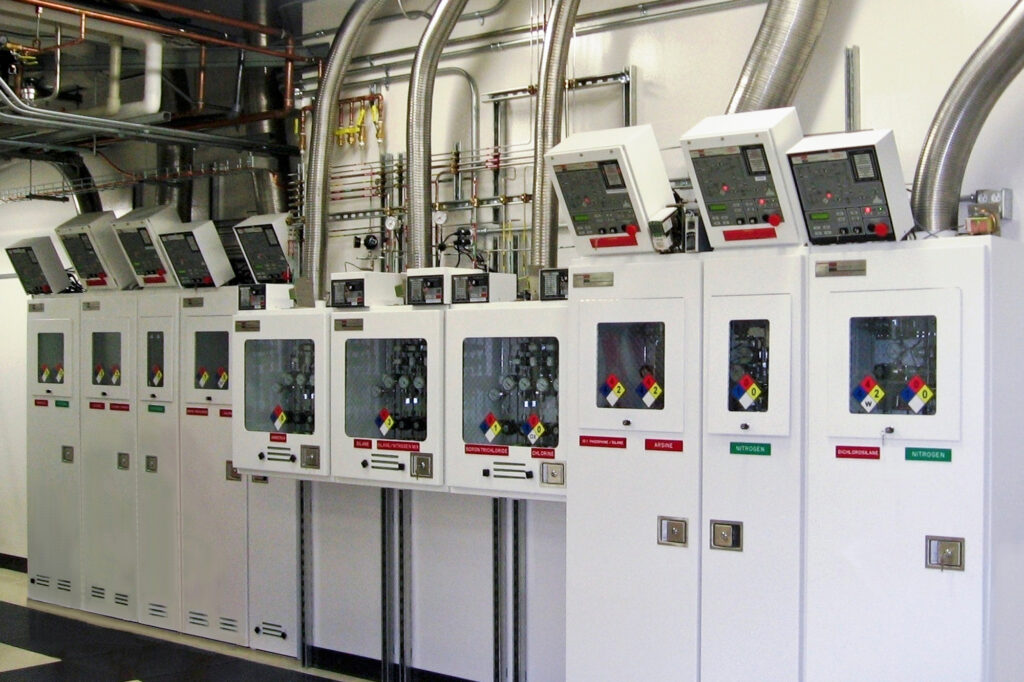
Safety Approval
Tracer Gas Testing
Tracer Gas Testing is crucial to gas delivery systems and chemical delivery systems. Furthermore, the testing also includes understanding of how the equipment is being ventilated.
This testing allows us to ensure the capture of toxic chemicals and flammable materials within enclosures. This testing is crucial to the development of your delivery equipment certification to SEMI standards and required by the semiconductor industry. Allow us to perform a third-party evaluation, testing and validation of your gas and chemical delivery systems.
If you’re looking for new and innovative ways to have your equipment meet tracer gas testing and pass ventilation requirements, then contact us now.
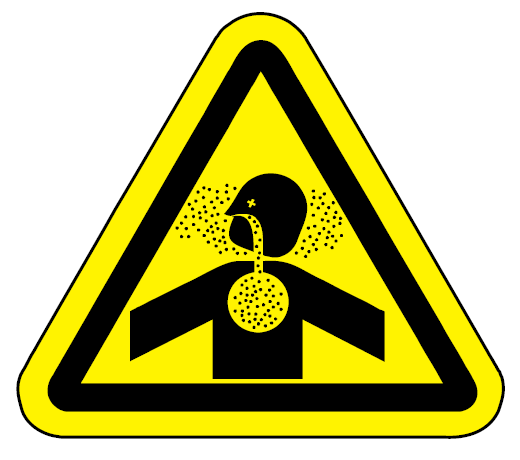
Frequently Asked Questions
What is the most commonly used tracer Gas for Leak Detection?
SF6 or Helium are very commonly used and have a wide range of applications; however, there are limitations. These limitations include costs, gas density and background contamination of the same or similar gases.
What Standards Apply?
There are many standards and we can help you to determine what is right for your equipment and your industry. As an example, SEMI S6 is the environmental, health and safety guideline for exhaust ventilation of Semiconductor Manufacturing equipment. It refers to the optimization of exhaust ventilation. This is our primary testing service.
How do I get Testing done?
First, you need to understand your equipment, how it's used and which chemicals will be used in it. Next, you will need to have a basic understanding of which standards are required. Typically, we apply SEMI S6 for the semiconductor industry. Other standards do exist and therefore, we recommend contacting us for confirmation on which standard is appropriate for your equipment. The next step is to get a quote. This will help you to scope, understand and prep for your testing. Additionally, you will need a complete piece of equipment with exhaust that exits the building and doesn't come back in. Once these are in place and confirmed, send a purchase order and we can schedule your testing.
Who needs tracer gas testing?
If you are building a system that generates toxic, flammable, pyrophoric, noxious or odorous materials as part of the process, and these materials are released or may be inadvertently released during processing, service, maintenance or upset or incident, then you will need this testing. If you are unsure if your equipment needs testing, reach out to us through the contact form below, and we will support you in understanding if you need this testing or not.
Why do I need Testing?
Most semiconductor facilities, pharmaceutical manufacturing and chemical processing facilities all require proof of exhaust capture of dangerous toxic, flammable and pyrophoric materials. Proving that your exhaust capture works, reduces risk of explosion or fire and reduces risk of exposure of employees to toxic materials. All semiconductor facilities required tracer gas testing for any equipment using these hazardous materials. You will need testing if you expect to deploy equipment into these industries.
What Safety Approvals do I need for gas Cabinets and Gas Delivery systems?
A broad range of safety approvals are available for this type of equipment, from SEMI S2 certification to CE marking and NRTL/UL Listing or approval. Your equipment may bare many different types of certificates and markings, which shows safety approval for exhausted enclosures based on tracer gas testing.
Process
We help walk our clients through the process to design based on the standards that it will be tested to and need to comply with in order to enter your desired market.
Timeline
Our basic timeline for Tracer Gas Testing is about three weeks for the full process after the PO is received. Each piece of equipment is different and we can quote your specific equipment.
Cost
There are factors that you can anticipate will add to the cost and can be planned for in your budget.
Resources From The Field
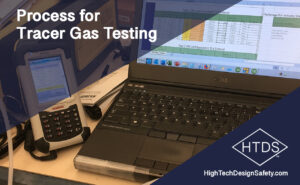
Process for Tracer Gas Testing
What is the process for tracer gas testing? Often we find it is beneficial for our clients to have an overview of the whole process so that they can budget and plan for upcoming testing, certification and approvals. This makes sense given that there are many phases and steps when taking a product to market.
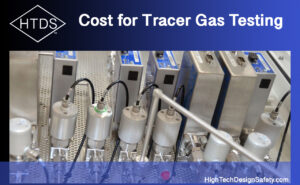
Cost for Tracer Gas Testing
Today we will explain the factors that go into the cost of tracer gas testing and what you can anticipate when creating your budgets for acquiring safety approvals to get your product to market. https://www.youtube.com/watch?v=MrcCrtjdNr0 Link to video also available here: https://youtu.be/MrcCrtjdNr0 What you Can Expect From the Video and Blog Know the basic costs
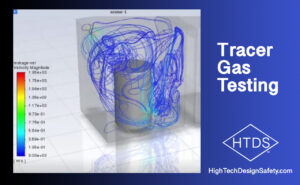
What is Tracer Gas Testing
Today, we are going to answer the questions, what is tracer gas testing and SEMI S6. This is one of the many services that we here at High Tech Design Safety, LLC. provide. Additionally, we provide SEMI S2, SEMI S8, UL Certification, NFPA 79, and other product equipment safety approvals and certifications. Furthermore, see our